All Around #12
Building up down under
Pioneering infrastructures are booming in Australia and New Zealand. Ambitious transport, supply and disposal projects are already being made a reality. Many new projects are in the planning pipeline. Learn more about innovative traffic and utility tunnelling in Oceania.
35 years of expertise

A shared history of breakthroughs
Herrenknecht tunnelling technology gained a foothold on the 5th continent in 1986. Contractors are using Herrenknecht technology in over 100 projects. 86 project breakthroughs have already taken place. Newly built infrastructure: over 260 kilometers of new tunnels, pipelines and pipeline networks.
At a glance
All around down under
Current tunnelling milestones
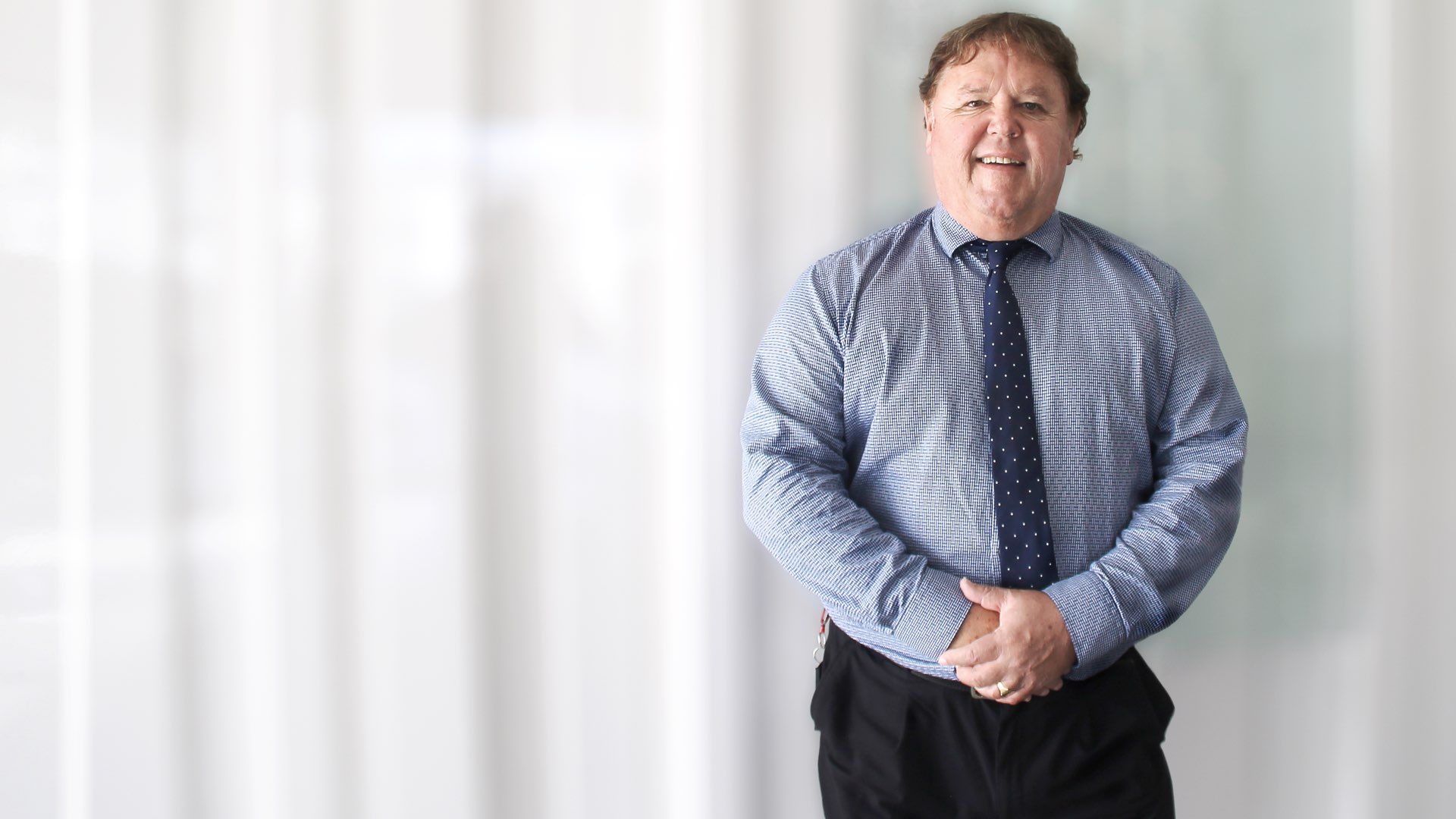
„Using Herrenknecht Micro TBMs, pipelines were constructed with minimum disruption to Auckland’s regional arteries. Direct Pipe® has even created more installation possibilities in different geology.“
John McCann, Projects Manager – Construction Delivery, Watercare Services Limited

„Mega projects require resilience and professionalism, qualities shown every day by Herrenknecht team. With all 4 TBMs launched, our ongoing relationship will become even more integral to our success.“
Etienne Baranger, Western Precinct Director, Melbourne Metro Tunnel Project CYP Design & Construction (Bouygues Australia, Lendlease, John Holland)
All set to go
Mission Future
Australia and New Zealand are launching bold and groundbreaking infrastructure programs for the coming decades. They are expected to trigger far-reaching impulses for economic and social prosperity. A report on hands-on shaping of the future.
Portrait Herrenknecht Australia

Passionate tunnel engineer between continents and time zones
Charles Howarth is Managing Director of Herrenknecht Australia and the key contact for customers and their underground missions. A short story about the development of the Herrenknecht subsidiary in Australia.
Contact
Ambitious project plans down under?
We’re ready to start!
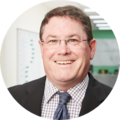
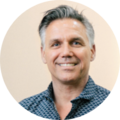
All around online magazine
TEAMWORK INTO THE DEPTHS
The mining experts of the Nezhinsky Mine in Belarus are currently rewriting mining history using a new type of shaft sinking technology.
MoreBuilding up down under
Pioneering infrastructures are booming in Australia and New Zealand. Learn more about innovative traffic and utility tunnelling in Oceania.
MoreHerrenknecht at bauma
Herrenknecht presented its extensive portfolio at four booths demonstrating where the journey in tunnelling is going.
MoreTOGETHER IN EVERY DIMENSION
Find out how mechanized tunnelling from Herrenknecht shapes the world of tomorrow.
MoreFOCUS ON PIPELINE
Along the lifeline pipeline. In any terrain.
Efficiently cross under tough key sections.
HARD ROCK TUNNELLING
In rough environments, the realization of ambitious plans calls for straight solutions and outstanding performance.
MOREEVERYTHING FLOWS
International championship alliance completes world class metro tunnel project in Doha in record time
moreTHE BREAKTHROUGH REMANUFACTORY
Re-using premium technology calls for professional remanufacturing. This opens up new potentials for our industry.
moreConnecting Continents
True teamwork and high tech from Herrenknecht unite Asia and Europe below the sea
MOREHerrenknecht All Around is a digital magazine published by the Herrenknecht Group. In our online issues, reporters and photographers feature exciting and latest stories from the global world of mechanized tunnelling.
Subscribe to our mailing and receive information on the current issues.