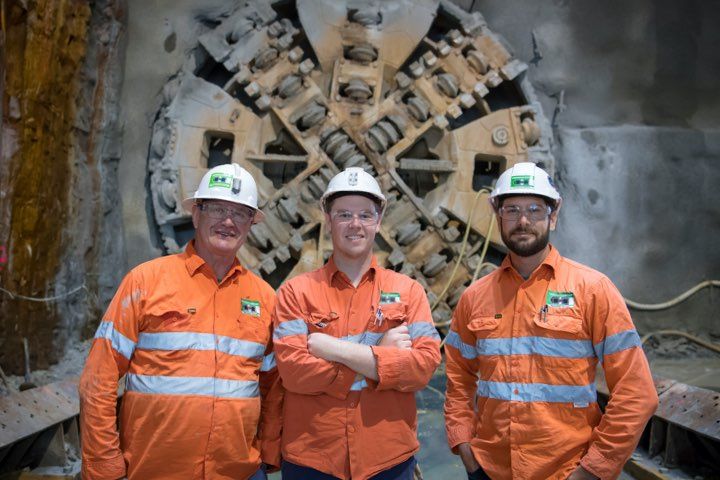
Jurek Szimmuck (right) knows: “The success is primarily thanks to the team spirit on site.“
On the evening of March 16, 2020, Herrenknecht’s project manager Jurek Szimmuck can finally breathe a sigh of relief at Sydney Harbor: after crossing the harbor basin, Mixshield-TBM 'Kathleen' makes its final breakthrough in the second construction phase of the Sydney Metro. The cutting wheel comes to a halt at Blues Point, within sight of the Harbor Bridge and the world-famous Opera House. Martin Bell, Plant Manager of the joint venture JHCPBG (John Holland CPB Ghella), summarizes the project as follows: “Our own people were very happy with the design and operability of the machines. When the crew makes good progress underground, they like coming to work. And then the project is a success.” Feedback like this is crucial for Jurek Szimmuck and his colleagues. Then they know Herrenknecht has truly accomplished their mission.
Starting in the Australian spring in 2018, five Herrenknecht TBMs burrowed through Hawkesbury sandstone over a distance of more than 31 kilometers. “Excellent machine availability of around 99 percent speaks for itself,” says Jurek Szimmuck. “The machines managed up to 85 meters of tunnel a day and 324 meters in a week.” The site crews and machine technology stepped on the gas for almost a year and a half. “This success is thanks to the team spirit on site,” said Szimmuck. “With our colleagues on the customer side, we felt like we were part of a big jobsite family. At some point we understood each other implicitly and complemented each other fantastically.” Leonardo Pia, Tunnel Manager of the contracting joint venture, wrote to the Herrenknecht team in this regard: “I believe the key of success for this project was more in the human factor side of the game. You’ve really been able to understand the best way to interact with us at all levels, from senior management to the field“
Herrenknecht already had a long history with the tunnelling professionals Down Under: in 1995 Herrenknecht received the first order for a large-diameter TBM (10.71 meters) for the Sydney Airport Rail Link. In the run-up to the 2000 Olympic Games in Sydney, a new rail connection between the airport and the city center was created for the international audience.